What Is a CNC Swiss Lathe and What Applications Are They Best Used For?
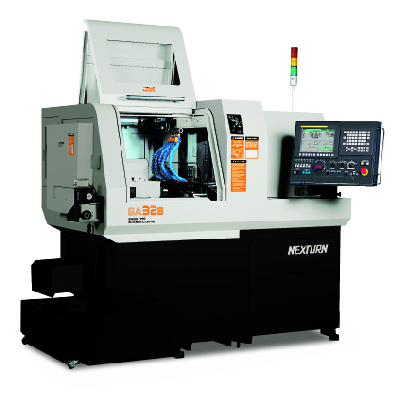
What Is a CNC Swiss Lathe?
Unlike a conventional lathe, a CNC Swiss lathe has a sliding headstock for the main spindle and a sub-spindle at the back so an operator can machine simultaneous processes to drop a part complete in two operations. The sliding headstock is unlike a conventional lathe because the material moves toward the tool, as compared to a conventional lathe where the tool moves towards and into the material.
The sub side is more of a traditional style to where it’s still a sliding headstock, but the axes are the same as a conventional lathe, so you’re still pushing the material into the tool compared to the tool into the material.
Why Do They Call It a Swiss?
The Swiss lathe originated in Switzerland and was first used to make fine threaded parts and small shafts for the Swiss watch industry. Later, the machines were used to make intricate gun parts. Although today’s machines may have far surpassed the level that made Swiss watches famous, the same basic concepts continue to be a vital part of the industrial landscape.
Today, a CNC Swiss type automatic lathe would be unrecognizable to early 19th century watchmakers. Their Swiss lathes used a disc cam to rotate tooling to a workpiece, which was held in place by a collet and supported by a guide bushing. Disc cams moved the tools in a radial motion while simultaneously altering the headstock position.
In recent years, CNC Swiss machines have quickly become a necessity and are considered value-added equipment for many component manufacturers. Unlike older lathes, CNC Swiss style lathe provide manufacturers with an invaluable competitive edge through:
In the 1970s, Swiss machines were vastly improved by replacing cams with computer numerical controls (CNC). Precision CNC machining (Swiss or screw machines) uses coded programming instructions to process a workpiece to specifications without intervention by a manual machine operator. With the addition of CNC, Swiss machine tooling began to include turrets, gang slides, and secondary spindles, improving speed and accuracy.
When parts are rotating at a speed of up to 15,000 RPM with live tooling up to 10,000 RPM and tolerances anywhere between ±0.0002” (±0.00508 mm) and ±0.0005” (±0.0127 mm), Swiss machines can support high volume requirements with just a single skilled machinist. That translates to more high-end quality parts in less time, which ultimately relates to a company remaining competitive.
Since then, continuing improvements in servo motors and controls, as well as the use of high-pressure coolants, have made Swiss lathes a requirement for making parts for many different industries that have high precision, speed and torque requirements.
How Do CNC Swiss Machines Work?
At the beginning of the turning process, the main spindle of a Swiss type cnc auto lathe will unchuck the workpiece, giving you the amount of stroke you need based on the length of the part. Through the use of the guide bushing, the bushing will continue to feed the material into the tooling to create the desired features.
Swiss lathes are best for length to diameter ratio parts, so if you’re running a 6” long part that is 0.20” thick, you’d have warping if run on a conventional lathe. But the same part being held in a guide bushing can be machined in one cut because the concentricity of cutting is being held by the guide bushing, allowing for excellent surface finish. The close geometry construction of the machine allows the tool to work within millimeters of the workpiece, reducing chip-to-chip time to a second or less.
Also, through the use of a guide bushing, a tool can take a heavier depth of cut on the part itself without jeopardizing tolerances. Then the machine does a pick off process with the sub-spindle side, and if there are any secondary operations on the back of the part that need to be done, it can be achieved here at the sub. The part is then dropped into a part conveyor that ejects it out the front of the sub, or utilizes a long-shaft discharge unit to where you are using the next piece of bar to be machined to push the part out the back of the sub.
How Many Axes Does a Swiss Lathe Have?
It can vary depending on the options. For instance, the Nexturn SA-20B is a simple 7-axis machine with 4 axes on the front and 3 axes on the back. The 4 axes on the front or main spindle side are X, Y, Z and C, and the 3 on the back or sub-side are X, Z and C.
Nexturn, and other brands of Swiss lathes, have options for a Y axis on the backside. Other models also have B-axes for use with angular drilling tools. That is how you stack axes based on options. Most conventional Swiss machines have anywhere from 7-9 axes.
What Makes a Swiss Lathe Different from a Conventional Lathe?
The difference would be the utilization of the guide bushing. The guide bushing supports the workpiece and greatly assists in maintaining precision throughout the cutting process. The guide bushing holds the workpiece so close to the tool that deflection due to the cutting force is essentially reduced to zero.
On a conventional lathe, the further away the cutting tool is machining material that is being held by the chuck, the lesser the stability is for the part being turned. Because of this, there is more of a tendency for chatter, vibration, whipping and poorer surface finish quality.
When cutting on a Swiss machine on the main spindle side at the guide bushing, your machining is very close to the guide bushing. In fact, typically it’s as close as cutting can be physically done in one spot, which is typically 0.20” (or 20 thousandths). This close proximity of the guide bushing to the cutting tools assists in keeping the piece extremely rigid allowing for an achievable high quality surface finish.
What Types of Applications and Industries Are Best Run on a Swiss Machine?
Accuracy, quick production times, and a reduction in variable costs have made Swiss machining the process of choice for a variety of applications and industries. Swiss lathes are ideal for turning applications with live tooling for cross-holes using milling, drilling, and or tapping, as well as parts that require high precision (accuracy) in high volume.
Once a Swiss machine is tooled up and ready to go, it should be able to hold tight tolerances of +/- .0005, basically giving the operator a thousandths tolerance. A Swiss machine also eliminates the need to remove the piece for secondary operations because you are able to drop a part complete, minimizing the amount of time a hand has had to touch the part. Live tooling on sub-spindles enables multiple machining operations on one machine, which reduces overall machining costs on complex parts.
With the ability to mill, drill, thread, polish and more, Swiss machines are capable of completing and dropping complete ready-to-ship parts. Additionally, with the right setup, the machines can often be programmed to run unattended on a lights out schedule.
Industries that require high precision metal machining include aerospace, defense, electronics, medical, and automotive, where exceptional tolerances, difficult geometries, and exotic materials and alloys are commonly used. Due to the extensive high-quality nature of the parts, certifications in these industries that are strictly adhered to for quality and reliability are best made on a Swiss machine.
Choose the Right CNC Lathe for Your Needs
If you need a CNC lathe, swiss type or otherwise, Absolute Machine Tools can help. Email info@absolutemachine.com or call us at (800) 852-7825 to learn more!