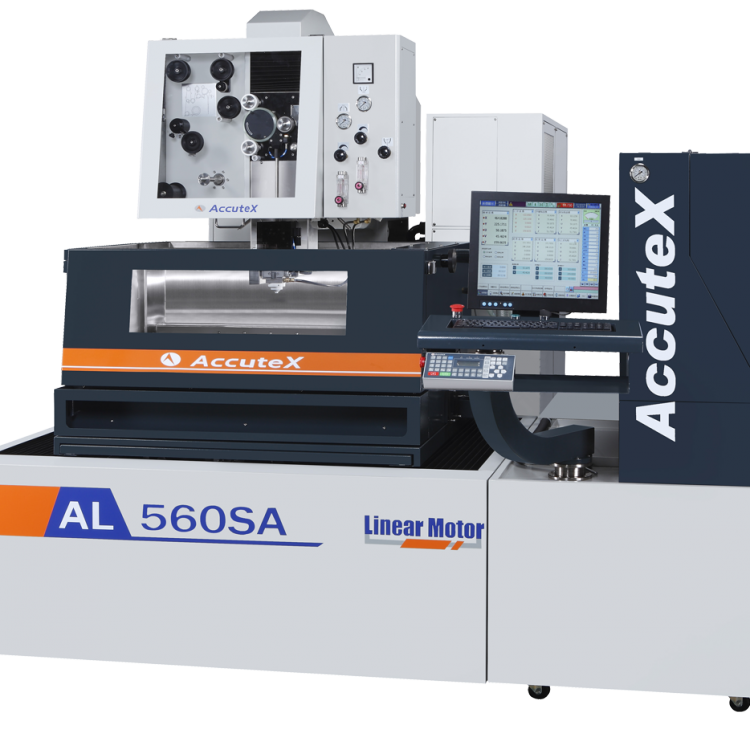
EDM or Electrical Discharge Machining is a manufacturing process that is based on the controlled erosion of conductive materials using an electrode. It was first achieved in the 40s, but has developed into one of the most precise and high-quality metal removal processes available. EDM machines are generally used to achieve very complex shapes in extremely hard metals such as tungsten carbide, titanium, and hardened tool steel alloys.
How does EDM work?
There are two types of EDM machines: Die Sinker and Wire EDM. The operation of both is based on the same principle.
An electrical spark is created between the workpiece and a charged electrode using dielectric fluid as the media to control the flow of current. The CNC-controlled machine brings the two electrodes close enough to ionize the gap and superheat the surfaces of the workpiece and electrode.
Once the necessary temperature is achieved, discharge occurs and the material is vaporized. Once the material removed the generator will shut off for a short period of time allowing the vaporized particles to be flushed away in the dielectric fluid. This process repeats itself over and over again at frequencies of approximately 100,000 times per second during rough machining cycles.
In the case of Wire EDM, the role of the cutting electrode is fulfilled by a precisely manufactured brass wire ranging in diameter from 0.0005” to 0.013”. The wire is guided through the workpiece using precision diamond dies at both top and bottom of the workpiece. Sinker EDM typically uses a custom machined electrode made from various materials such as Graphite (carbon), Copper or more exotic materials such as Copper Tungsten.
Why is an EDM ideal for die/mold applications?
The manufacturing of highly tailored dies and molds call for extreme accuracy. As they feature demanding design points such as sharp internal corners, narrow slots, deep ribs and other intricate shapes. There is no other tool that can achieve the high-precision machining required for the manufacturing of die and mold parts without segmenting the features into simpler shapes.
Moreover, the EDM’s ability to achieve such a fine surface finish, surface integrity and high precision minimizes or eliminates the need for polishing and other secondary processes. Finally, dies are usually made out of very hard steel alloys making it necessary for roughing and or finishing prior to heat treatment dramatically reducing the accuracy of the detail. This typically translates into custom hand work, spotting and fitment which also makes repair and maintenance of the tool time consuming and costly.
Why choose AccuteX for Die and Mold Manufacturing?
AccuteX EDM machines are known for their reliability and high-quality results thanks to the following exclusive technologies:
Intelligent Discharge Unit – The discharge unit dynamically identifies changes in workpiece thickness and flushing conditions, allowing it to adjust its operation parameters to maintain a stable cutting speed. This makes AccuteX machines able to cut irregular thickness objects about 34% faster than most EDMs.
High-Performance Cutting: AccuteX EDM machines were tested to be 20% faster cutting up to 50% faster than competitors EDM machines when cutting plates that exceed 200 millimeters of thickness.
Intelligent Arc Control: Intelligent corner and arc control is active from roughing to finishing cycles controlling critical functions to dramatically improve corner accuracy and finish.
SD Master: SD-Master improves machining repeatability hole to hole,
machine to machine. No need to customize cutting conditions and program wire offset. SD-Master ensures accuracy and repeatability from one machine to another. High-speed machining is stabilized and wire breakage is reduced making cycle time and deliveries reliable and predictable.
Reliable AWT: The most reliable AWT on the planet
Contact Absolute Machine Tools today at 513-701-5550 to learn more about our AccuteX Wire EDM machines!