Job Shop Automation Leaping Forward
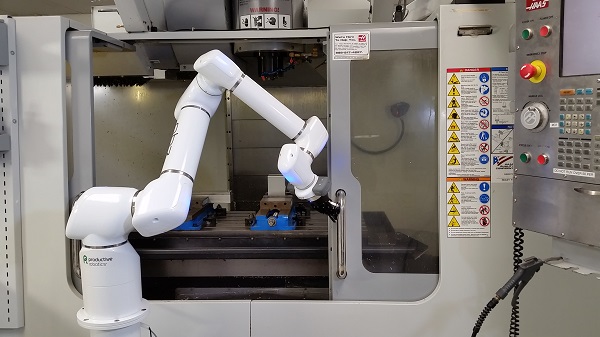
With the combined influence of Industry 4.0, the continued lack of skilled manufacturing labor and the COVID pandemic, the automation of job shops is taking an accelerated leap forward.
The availability of more customized robotic and material conveyance options than ever is helping smaller manufacturers produce more while moving operators to more value-added tasks. The surging demand for personal protective equipment (PPE) coupled with a need to protect workers has also ramped up shops’ automation efforts.
The benefits of automation, clearly amplified during the pandemic, were summarized neatly by Courtney Ortner, chief marketing officer of Absolute Machine Tools: “With the use of cobots (collaborative robots), you have a work partner and you don’t have to worry about social distancing. Also, many shops are losing workers to quarantine, so this allows a shop to continue to run even with the loss of staff. And we can’t forget lights out abilities are more common because of the use of automation; even with a cobot, you can set a job up on a Friday night and by Monday morning it’s done — oftentimes allowing you to be ahead of your production cycle.”
Assessing Need, Adding Speed
Understanding a job shop’s automation needs begins with a thorough evaluation of the volume required to increase productivity.
When hired by a client, says Absolute’s Ortner, “we do a system layout, decide best practices to automate — conveyor systems, robots, raw material handling, finish part handling — then design it in CAD to ensure all the pieces fit in their floor plan, all the while working within their budget.”
In addition to offering an array of the standard equipment for job shop automation, from cobots to part handling to monitoring, she added, “we are offering a turnkey package. We source what we feel is the best solution and work with those suppliers to ensure success.”
Absolute’s experience in sourcing the right equipment clearly pays off, she noted. “One client using an OB7 cobot is getting 20 percent more efficiency and a lot less scrap in a shift. They are able to reduce delivery times by two weeks on this particular run, which opens up the machine/cell for additional work for a higher ROI. Also, because they don’t have to do repetitive tasks as often, there are less workers compensation claims for the company — and they don’t call in sick as often either, saving the company a lot of money.”
As others have found, the increased availability of operators for other tasks often means “they have more time to contribute to the overall processes, like quality-control checks. They are more involved in process management rather than simply pushing buttons and are less bored and fatigued.”
Job Shop Automation Can Be Affordable
Obtaining those benefits can be surprisingly cost friendly, she added. “Our cobot line from Productive Robotics starts at $34,900 for the basic CNC package. You can go from basic CNC package and upgrade to a fully integrated cell using several cobots, conveyors, in-process gauging and part presentation methods.”
Get help adding automation to your job shop! Contact Absolute Machine Tools today at info@absolutemachine.com.