Delivering Big Gears Fast at Brevini Wind
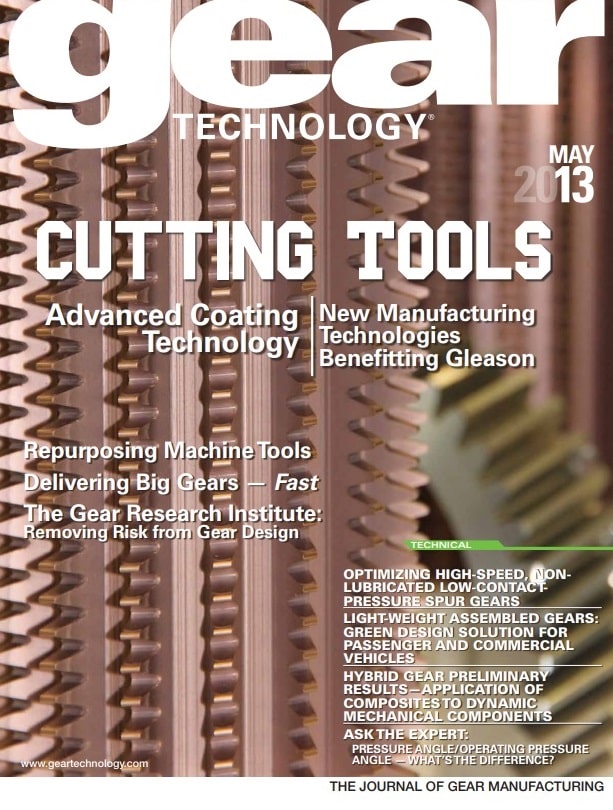
When a customer needed gears delivered in three weeks, Brevini Wind partnered with Absolute Machine Tools to get the job done.
Recently a South American manufacturer needed four large, double internal replacement ring gears for its sugar mill, and the OEM who provided the originals was quoting eight months lead time. Unfortunately, they needed their parts faster — much faster. Looking for alternative manufacturers, they called on Brevini Wind, in Yorktown, IN.
“We were challenged to produce four large, double-internal ring gears in three weeks,” says Dale Harder, director of facility operations at Brevini Wind USA. Each of the large planetary components contained two internal gears. On one end was a 12-module, 76-tooth, 282mm face width internal gear. On the other end was an 8-module, 116-tooth, 140 mm face width internal gear.
The biggest challenge in producing these gears so quickly was figuring out the tooling, Harder says. Getting new cutting tools would have taken too long, so they looked at previous projects for parts with similar geometry to see if they could re-use existing tools. As it turned out, they had gashing cutters for previous internal gears with modules of about 12.1 and 7.3. Banyan prepared CAD drawings of both internal gear elements, and then analyzed the existing cutting tools and stock conditions that would result. After their analysis, Witte had good news and bad news. They’d be able to cut the 12-module gear with existing tools, but not the 8-module.
“For the larger internal gear element, we were fortunate enough to have a duplex profile milling tool for an application whose geometry was close enough to semifinish the internal gear,” Harder says. “Banyan Global provided Brevini Wind with a CAD model of the cutter profile versus the finished tooth profile, illustrating the maximum depth of cut that could be made while maintaining sufficient stock for finishing the gear teeth via a subsequent internal gear grinding process.”
But they still had some work to do. Even though Banyan demonstrated that they could produce the geometry they needed with the existing cutting tools, Brevini Wind still needed a little bit of ingenuity to make it work, Harder says. “Because there wasn’t sufficient room for the cutter radius to break out without hitting an adjacent shoulder in the part, our gear machining leader, Chris Hayes, devised a process to first radially infeed utilizing our Gleason-Pfauter P2400 hobber at the furthest possible point on the facewidth before beginning to feed axially up the facewidth.”
So Brevini Wind could make the 12-module internal gear with existing cutters. But what about the other side? Unfortunately, Banyan’s analysis revealed they had no cutting tools available with close enough geometry. “So we elected to grind the gear teeth from solid using our Gleason-Pfauter P1600G gear grinder,” Harder says. “This permitted us to generate the required gear geometry relatively quickly.”
Harder explains that even though grinding from solid is a much more time-consuming process—in this case six hours versus the one hour that would have been required for gashing—it could be done using inexpensive, off-the-shelf grinding wheels that didn’t require any additional wait time.
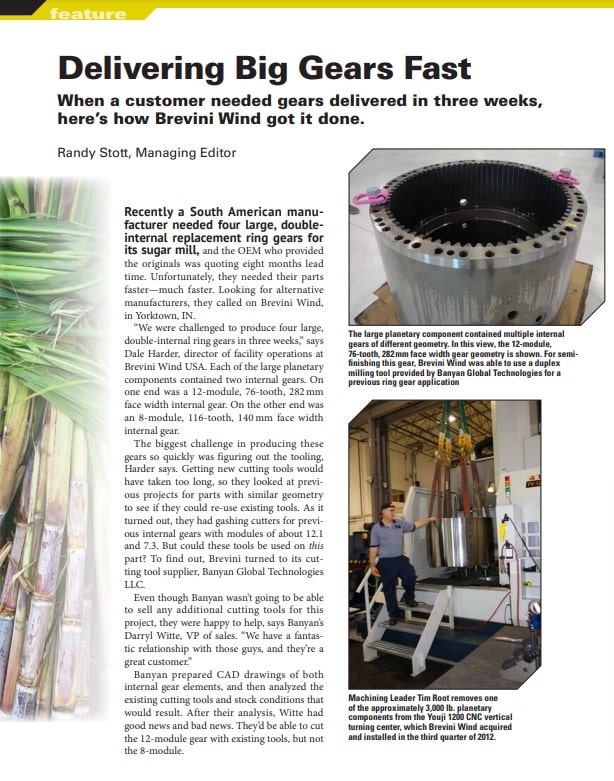
After rough machining, the parts were inspected, stress relieved and inspected again in Brevini’s climate-controlled inspection lab. Having heat treating and metallurgical facilities in-house greatly enhances Brevini Wind’s ability to turn parts around quickly, Harder says, and it also allows them tight control over every process.
“Due to considerable material removal from the required machining processes, Brevini Wind elected to stress relieve all of the large planetary components prior to finish machining critical dimensional characteristics and gear geometries,” Harder says. “Brevini Wind performed analytical inspections on the internal gear tooth geometries before and after the stress-relieving process to determine the level of dimensional movements that occurred,” Harder says. “The information was utilized to confirm green machining dimensional targets that will provide minimal stock removals for the post-heat treating finish machining processes.”
Those finish machining processes included not only final gear machining, but also finish turning on the company’s newly acquired You Ji YV-1200ATC CNC vertical turning center. With the live tooling capabilities of the You Ji, it was also possible to process the numerous M36 threaded holes that were required around the part end face. The holes were drilled and the M36 threads were generated using circular interpolating thread milling technology instead of conventional taps. “The result was very precise threads, excellent size repeatability and no broken taps,” Harder says.
In the end, Brevini was able to provide these parts on schedule for a customer with a very tight deadline. “Because of our equipment, expertise, innovative thinking and some very dedicated employees, we accomplished the mission,” Harder says.
At Absolute Machine Tools, we take immense pride in partnering with manufacturers to empower their success. As demonstrated in Brevini Wind’s remarkable gear production saga, our commitment to providing top-notch equipment like the You Ji YV-1200ATC is unwavering. We understand the challenges faced by manufacturers in meeting tight deadlines and pushing the boundaries of innovation. That’s why we strive to offer cutting-edge technologies that unlock new possibilities, enabling our partners to achieve remarkable feats and surpass their goals. We believe in the power of collaboration and are dedicated to supporting manufacturers every step of the way. Together, we forge a path towards excellence in the ever-evolving world of gear technology.