We’ve all been told “less is more”; however, in the case of having a 7-axis cobot, more is definitely better. OB7 collaborative robots from Productive Robotics come standard with a built-in 7th axis.
Most people overlook the abilities of the 7th axis, especially when referring to cobots. However, the freedom that the 7th axis provides far exceeds the fact that it can reach around the machine door to load/unload parts while performing machine tending operations.
We’ve all been told “less is more”; however, in the case of having a 7-axis cobot, more is definitely better. OB7 collaborative robots from Productive Robotics come standard with a built-in 7th axis.
What Exactly Is the 7th Axis?
The official term “7th axis” typically refers to an additional linear axis that can be “added” to a robot or cobot to provide extra flexibility and range of motion. This definition is incorrect for OB7 cobots from Productive Robotics because they come standard with a 7th axis built into the robotic arm. There’s nothing to program or add internally or externally; it just comes standard.
OB7 facilitates true, full human-like control and movement, plus open mobility in and around obstacles such as the machine door, table, chuck, vise and part. This ensures consistent operation even in tight spaces or small work environments.
Why a 7-Axis Cobot Beats a 6-Axis Cobot
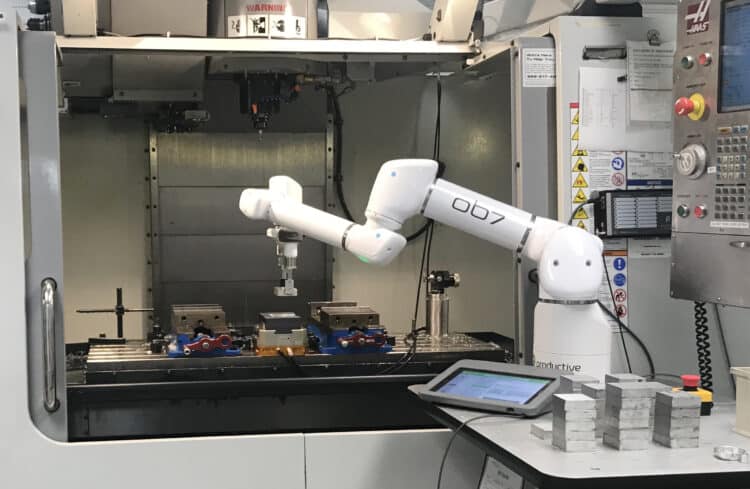
The biggest advantage to the 7th axis is that it allows full and safe access in front of the machine door area and internal work envelope, without impeding upon active space either inside or outside the machine. A 6-axis cobot must be set up in front of the machine door, blocking access for an operator to perform other necessary tasks that may require attention during the machining process, such as replacing inserts, blowing off chips and coolant, or making fine tune adjustments.
Why is this important? To have access to these areas using a 6-axis cobot would mean that the operator would have to stop the program, move the cobot out of the way, and perform his/her necessary tasks. Once the tasks were completed, the operator would have to move the 6-axis robot back in front of the door and reteach the way points or make internal adjustments to accommodate the cobot’s new placement. These types of setbacks waste time and money but can all be avoided with a 7-axis cobot.
Advantages of 7-Axis Cobots
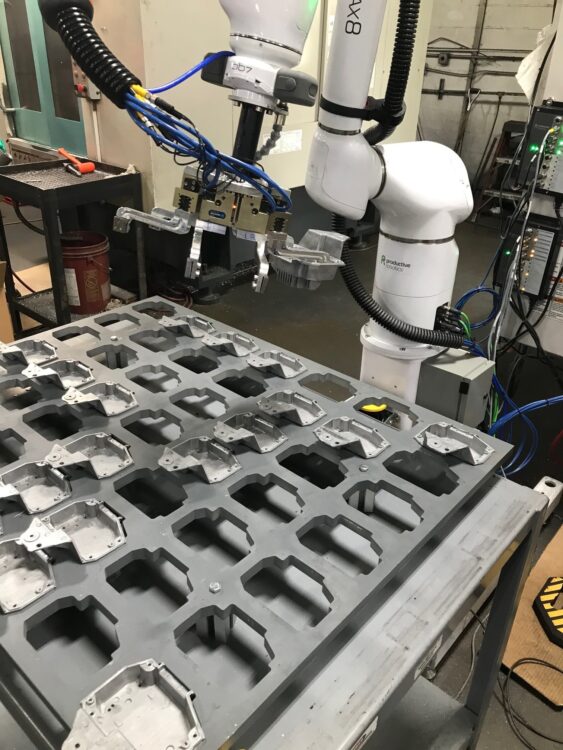
Here are some other advantages to consider when comparing a 6-axis cobot to a 7-axis cobot such as OB7:
Increased Machine Reach and Workspace
A 7-axis cobot enhances reach and frees up additional internal workspace area by allowing the cobot arm the flexibility to move in and around obstacles. As in the case of machining centers, there may be multiple vises set up for various machining operations. Having the flexibility of a 7th axis allows for more freedom of motion to safely avoid these obstacles, providing for additional productivity.
Increased Floorplan Space
The 7th axis allows more placement opportunities than a 6-axis cobot because it does not have to be positioned in front of the machine door. This is especially beneficial in compact floorplans and small work environments to accommodate the presence of an operator as well as the cobot.
Versatility
A 7th axis allows the robot to move along a longer path, making it more versatile to perform additional tasks, such as machine tending various workstations within the machining envelope.
Complex Tasks
Some tasks may require a combination of movements along multiple axes. A 7th axis enables OB7 to perform more complex motions such as short and long intricate movements or manipulation, especially when paired with a dual gripper or other end-of-arm tooling mechanisms.
Improved Obstacle Avoidance
A cobot equipped with a 7th axis naturally has an extended range of motion. Unlike 6-axis cobots, it allows for improved maneuverability and the ability to avoid obstacles in its path. This is especially important in a collaborative environment where the cobot needs to navigate around humans or other objects assisting in the automation cell.
Enhanced Productivity
The increased flexibility and reach provided by the 7th axis can contribute to improved productivity by reducing the need for manual human intervention or repositioning of a particular workpiece. The 7th axis allows the cobot to cover a larger area within the work envelope, avoiding the possibility of frequent adjustments by an operator.
Multi-Cell Workspace Areas
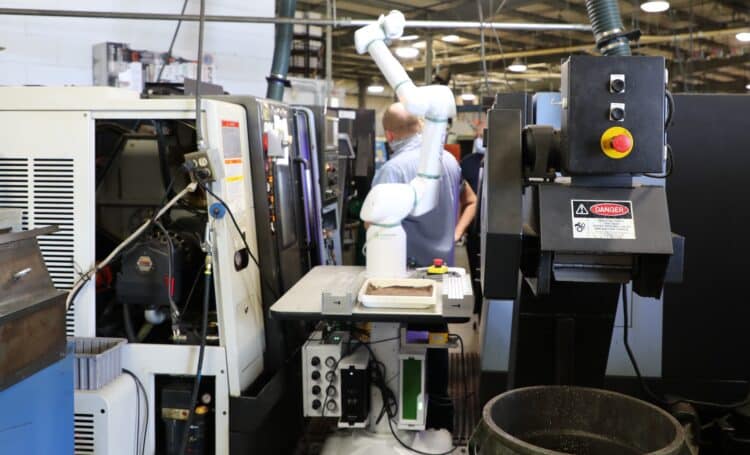
In manufacturing environments, a 7th axis can help optimize the layout of multiple work cells. Having the extra degree of freedom allows for optimized placement of the cobot relative to single or multiple cell workstations. As expressed above, the range of motion with a 7-axis cobot is much greater than a 6-axis cobot. It just makes sense that the 7th axis can better tend to multiple machines, making for one complete automation cell that includes multiple machines rather than having to invest in a second cobot.
Adaptability to Different Applications
The ability to add a 7th axis provides adaptability to different applications and industries. The 7th degree of freedom allows for customization of the cobot’s configuration to meet specific requirements, making it a more versatile solution than a 6-axis cobot.
Safety
One of the biggest concerns in manufacturing is safety. Collaborative robots allow humans to work safely beside them. However, if an operator is using a 6-axis cobot and he/she decides to make an adjustment or change in the work envelope, they may try and do this while the cobot is running. While all cobots have a force sensor that determines pressure when impacting an object, working in a tight restrictive environment can still to an operator. However, a 7-axis cobot can be placed off to the side of the machine door opening, allowing an operator more room and flexibility to make necessary adjustments more safely without potential impairment or injury because there isn’t an ample amount of room for both to work.

Opening a Broader Future
Now that you have read through this blog, it’s obvious that 7-axis cobots not only can do what 6-axis cobots can do, but much more. Even if the 7th axis isn’t utilized, it may be in the future. Manufacturers are always challenged to produce different more complex parts efficiently. Knowing that the 7-axis comes standard in all OB7 collaborative robots from Productive Robotics naturally gives the flexibility to be able to do more with a 7-axis cobot rather than a 6-axis cobot.
It’s important to note these advantages when considering a 7-axis cobot versus a 6-axis cobot when making important buying decisions, especially if the 7th axis is already available as standard equipment. Having the 7th axis doesn’t impede mobility of the cobot arm or cost more, but if you need it and don’t have it, then that’s another story.
Experience the Future of CNC Machining with 7-Axis OB7 Cobots
Are you ready to take your machine shop to the next level? Contact Absolute Machine Tools at info@absolutemachine.com to explore how automation with a 7-axis cobot from Productive Robotics can enhance your production efficiency and boost your profitability. Don’t miss the opportunity to transform your operations — reach out now!