Vision: Should You Go There?
For those that have not taken the first step to implement 2D, 2.5D, or 3D vision into their manufacturing processes, it can be intimidating. So how do you start and on what process?
The answer to that question is somewhat simple. Make the first right turn in your journey and ask yourself, โDo you have employees physically conducting quality control inspections on a regular basis?โ
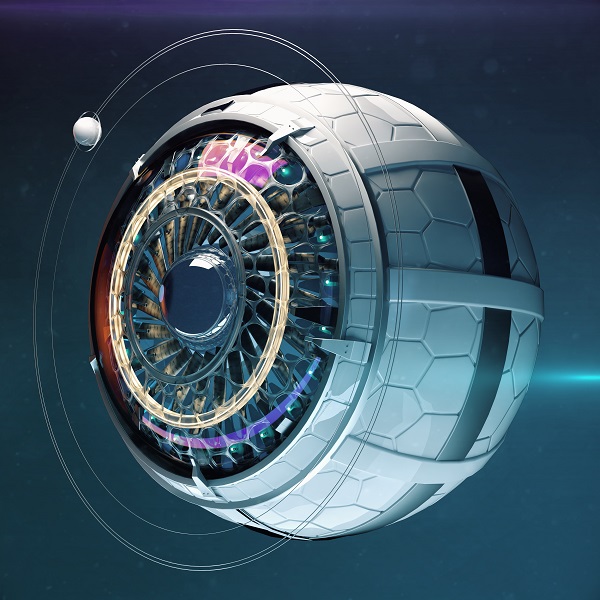
Why choose that process to start with you ask? Because every shop must perform some type of QC, making it a universal task that is often done manually with either your trusty calipers or on a CMM. Vision today is simpler than ever because of how fast AI is evolving. It is faster than most of us can keep up with. Also consider how aggressive vision OEMs must be to keep up with this ever-evolving technology to make it better, faster, and easier, especially before their competition does.
Today, automation end-users are expecting more by demanding simpler user-friendly solutions from vision OEMs. So, before you shake your head and say that vision does not have a place in your manufacturing processes, think again.
Referencing back to the first question, โDo you have employees physically conducting quality control inspections on a regular basis?โ Think about the amount of time it takes for someone to manually pick up a part and inspect it with the simplest form of QC, the trusty calipers. Then, documenting the measurements in a log or journal and returning to this process over and over throughout the day. How many more bad parts may have been produced during the inspection, documentation, and returning timeframe?
Now letโs consider using a CMM. Think about this โ the operator picks up a part, walks it to the air-conditioned QC room and places it on the CMM. Even if the CMM is already set up to inspect the part, the time it takes to properly position the part on the table, start the inspection and measuring process, analyze the data, and walk back the machine to adjust can take a considerable amount of time. How many parts and how much material might have been scrapped if the part is out of tolerance?
Now think about the process if a robot was picking up the part and inspecting it with either a 2D or 3D vision system. How fast do you think that process might be completed? Actions such as downtime, re-programming, and other adjustments to ensure tolerance have a measurable and quantitative negative impact on any jobโs ROI. Constant QC checks are always a debit to COGS. Then consider the value-added tasks your operator could have been doing while the robotโs vision system was checking parts. All these factors can add up to leaving money on the table.
But wait โ thereโs more!
What if your vision system could collect and analyze the data matrix of your part, and instead of stopping or alarming-out, automatically make corrections to the machineโs PLC? This is called process optimization, and the best part is you donโt even have to be there to know adjustments need to be made. You will see it in the data report when you get to the office in the morning, after youโve had your coffee.
Differences Between 2D & 3D Vision
There are a multitude of services both 2D and 3D machine vision systems can streamline; the most common use is mentioned above. But vision can also perform inventory management, robot guidance, material handling, assembly verification, recognition and identification, packaging, and bin picking in structured and un-structured environments with a diverse field or range of objects (different size parts on one conveyor or bin). And letโs not forget absolute real-time data collection. Manufacturers are using real-time data to make strategic decisions to remain competitive, and more and more end-customers are expecting manufacturers to share data for historical information on parts production. Thatโs a lot of applications that can be done quickly using process optimization, and it will have a positive effect on throughput. So, once youโve decided on the task, ask yourself, โWhich degree of vision will benefit this job most?โ
2D vision is typically faster than 3D because of its algorithms, data processing, and image acquisition. However, 3D vision works better on more in-depth complex geometries. 2D vision can perform complex bin picking of random parts and place them on a conveyor in a particular orientation; however, 3D vision is best if multiple touches and movements need to take place, especially if the part is delicate. 2D vision can handle picking random sized shaped parts on a conveyor, but if there is significant depth to the parts, then 3D is best. If the jobโs life cycle is a fixed period of time with voluminous parts, 3D vision is typically the answer because it can better apply color to the various parts to differentiate one from another.
Human Vision vs. Machine Vision
Human vision is best used for qualitative interpretation of an unstructured and/or complex scene. Our eyes are limited in size, and therefore have limited light absorption and frequency ability. The pupil diameter is also small, although it can change size depending on the brightness of the atmosphere, but for the most part is also limited.
The human eye retina accepts an image. Sensory input flows through the retina into the visual cortex of the brain. The cortex parses the information in an immeasurable amount of speed to recognize the object(s). But the human eye cannot accumulate light over long periods to intensify faint or distant images, and whatโs more, the eye cannot store an image for future reference.
Conversely, machine vision excels in quantitative measurement of a structured scene because of its speed, accuracy, and repeatability. Therefore, a production line using vision can inspect and identify thousands of parts per minute. It is also why machine vision can be used in high resolution for recognizing details in objects too small to be seen by the human eye.
Vision Drives Down Manufacturing Costs
It only makes sense that removing the human component of parts being tested, handled, or observed for inconsistencies prevents damage and reduces maintenance time and costs associated with wear and tear on mechanical components. It is also proven that machine vision adds a positive safety component to the manufacturing process by reducing human involvement, which increases operational benefits. Moreover, it prevents human contamination of clean rooms and protects workers from hazardous environments. All these mentioned are cumulative to increased throughput, which is always a significant driving factor in manufacturing.
Integrating vision into day-to-day manufacturing is no longer on the horizon, and it isnโt about to go away any time soon. Machine vision has arrived and is being integrated into manufacturing processes more and more each passing day. Visionaries implement forward thinking. Forward thinking is what drives American manufacturing. Integrating vision as a standard will be no different.
Partnering with a vision provider that is veteran to the CNC machine tool industry is smart forward thinking. The A+ Automation Team at Absolute Machine Tools is qualified in 2D, 2.5D, and 3D vision systems through OEMs such as Cognex, Keyence, Omron, and many more. For more information or help in deciding the best cost-effective automation solution is for your company, contact us today at info@absolutemachine.com, or call us at 800-852-7825. We are Absolute and we are here to help!