How is the Work Staged? It Should Be All Part of the Master Plan
Most manufacturers don’t understand — and sometimes underestimate the importance of — staging the work the cobot will handle. This is one of many reasons why automation projects fail before they start.
Often times, manufacturers are sold on buying a cobot for a project without first discussing the manner in which the part is going to be presented for handling. Suddenly, there’s a head scratching moment, and that’s when frustration first sets in.
But it doesn’t have to be this way. There is a right way to plan for a proper cobot implementation. How? By creating a comprehensive “Scope of the Project” that fits the master plan.
Where Will the Parts Be Placed?
Once a manufacturer decides they want to buy a cobot, they should then discuss the parts they plan to set up in registration with the cobot distributor. Will these parts be stacked on the cobot’s table that is attached to its stand? If that won’t work, what contraption will? Are the parts going to be somewhat symmetrical and placed next to one another in nice neat stacks, or will they be piled up willy-nilly in a bin?
Where Will the Cobot Be Situated?
Another thing to consider is the placement of the cobot. Where will the parts need to be staged for the cobot to reach? Will the cobot need to be set up in front of the machine’s door in order to accept the part in registration to properly load/unload the machine?
Oh boy! This raises another concern, as it will inhibit the operator from accessing the work envelope. If that’s the case, that’s when a 7-axis cobot can really help.
But then we’re back to figuring out how to stage the parts in registration. These decisions are why creating a comprehensive “Scope of the Project” becomes a catalyst for a successful master plan.
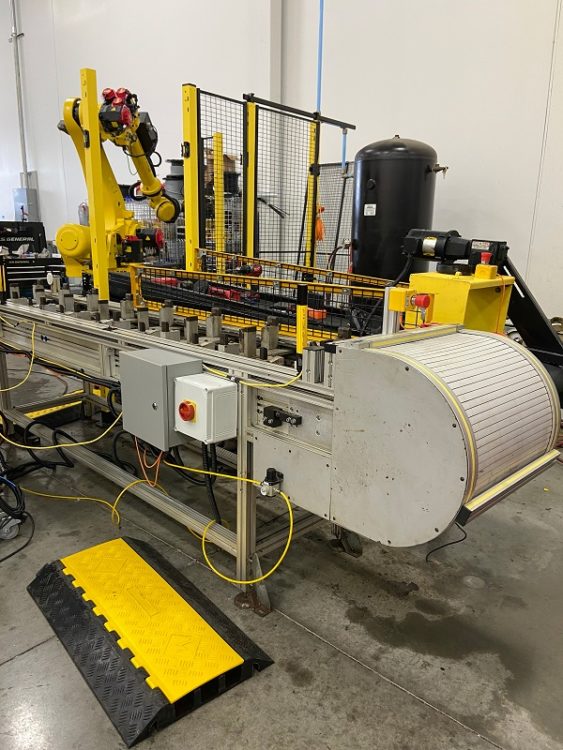
Finding the Best Way to Present Parts to Your Cobot
There are hundreds of ways to present a part to a cobot. Cobots require fixtures to either be purchased or built that will hold parts in registration. This is a work-holding cost that many potential customers don’t realize they will have to incur.
Fixturing can be as simple as lining up the parts in a tray, chute, or on a table, or as complex as picking from a bin or setting up automatic conveyors. This is not something a manufacturer should have to decide on their own because it’s not what they do day-in and day-out.
So how do you figure out what the best part presentation method and approach are to your process? That’s where we come in. Our A+ Automation Team at Absolute Machine Tools will work with you to explore different presentation options.
In some cases, customers already have presentation equipment that they want to resurrect. If not, then our A+ Automation Team will explore the best options and include it in the “Scope of the Project,” all while considering upper management’s budget for the master plan. Like anything else, it can be as complex as needed, or as simple as a manual contraption that an operator has to fill up throughout the day to keep the cobot continually loading and unloading parts.
Without experience, it’s not always obvious to know the simplest and most cost-effective solution. It will require some work and thought process up front, but will ensure a smooth and orderly installation and integration in the end, which makes everyone happy.
Email info@absolutemachine.com to get started!