In today’s competitive marketplace, manufacturers need to find ways to increase productivity and efficiency. One way to do this is by adding automation to the production process. Automation can help to improve quality control, reduce turnaround times, and decrease the amount of waste. For a CNC Swiss machine shop, automation can also help to improve accuracy and repeatability. In addition, automating the production process can help to free up employees’ time so that they can focus on other tasks.
Bar Feeder Systems for Swiss-style Machines
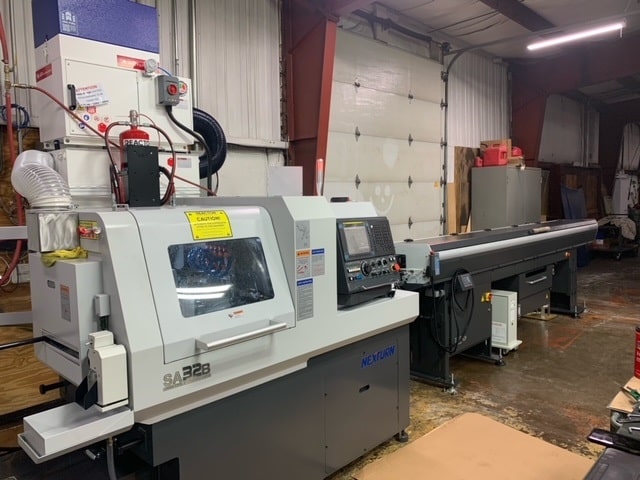
One way that a Swiss machine shop can automate their production process is by adding a bar feeder system. A bar feeder system is an automated device that feeds stock material into the machine. This can help to increase productivity by reducing the amount of time that employees spend feeding material into the machine. In addition, a bar feeder system can help to improve the quality of the finished product by ensuring that the material is fed into the machine in a consistent manner.
By simply adding a 12’ long bar feeder, one operator can tend 3-4 Swiss lathes at a time rather than employing one operator per machine. This lowers overhead costs and opens the possibility for the operator to perform other much-needed tasks.
Two primary types of bar feeders can deliver materials to Swiss-type lathes. Each is engineered to meet different needs.
Hydrostatic bar feeders
With hydrostatic bar feeders, the bar stock is held in a series of guide channels, which close around the material and lock it into place, keeping it stable. These systems generally have a 12′ stock capacity and are automatically reloaded with a magazine-type system.
Hydrodynamic bar feeders
Hydrodynamic bar feeders work by holding the bar stock in a tube that is filled with pressurized flowing oil. These systems typically require bar to be loaded manually, one at a time.
When deciding on a hydrostatic versus hydrodynamic bar feeding system for a CNC Swiss machine, you need to consider factors such as volume, material, and part complexity. If you need a bar feeder that can handle high-volume runs, hydrostatic is going to be your best bet. Hydrodynamic bar feeders are better for smaller part runs and one-offs. For more complex parts or difficult materials that need longer cycle times, hydrodynamic is the way to go.
Why Would a Company Buy a Bar Loader Rather than a Bar Feeder?
There are many reasons, however, three stand out the most:
Floor space
Many production houses or job shops don’t physically have the real estate it takes to have multiple 12’ long bar feeders next to each lathe on their floor, so they have to opt for a short loader.
Bar size
The cost for a bar feeder that can accommodate anything over 2.5” bar capacity is extremely expensive — anywhere from $70,000 up. If you’re running a $100,000 lathe, many can’t justify buying a bar feeder that competes in price with the CNC machine, so they will opt for a bar loader instead. Again, this is all predicated on budget for both the company and jobs being run with that setup.
Remnant pieces
Job shops are less likely to buy a bar loader with a Swiss machine because the remnant of your bar pushes out of the front. If the guide bushing is set properly then it is holding the bar snug enough it might not be able to push the remnant out. There is always a remnant piece of bar on each load to consider, which is normally 6-8” long dropping into the conveyor or bottom of the machine. A piece this size can dent the sheet metal or conveyor or even get stuck in the conveyor, causing serious damage.
If you are using a 12’ bar with a 12’ bar feeder, there will be anywhere from 6-8” of waste. This is normal because of the distance between the headstock and the front of the guide bushing. The remnant size is all predicated on the length of the part running. With longer parts, fewer parts can be cut off of one bar, so your remnant can be longer because you might not be able to get another piece out of the end of that bar. For parts that are 4” or under, typically there is only 6-8” of remnant left on each bar fed into the lathe. Many shops will keep that remnant piece and use the material on their conventional lathes, so the remnant material isn’t wasted.
Customers do care about the remnant and will ask Absolute’s applications department how much remnant we expect to see out of a time study. So, if you are going to get 136” out of a 144” bar, that’s an acceptable remnant for the amount of time it takes to drop these parts complete, meaning the potential waste of material is worth it when compared to the high quality of parts being produced in high volumes over a shorter cycle time. The efficiency and part quality factors when running a Swiss machine allows a shop to justify the 6-8” of remnant bar.
Doesn’t Automation Take Away Jobs?
With today’s skills gap and not being able to find qualified machinists, it’s best to automate as many processes as possible to have absolute control over production. Automation does not replace people, but rather fills employment gaps.
People are still needed to manage all the operations and manufacturing processes, such as:
Many people think automation is taking away jobs, but for the most part that isn’t the case. Automation helps companies to be more efficient and allows workers the opportunity to branch out and take on other value-added responsibilities instead of being pigeon-holed into standing by a machine and watching it run all day.
Get Help Starting Your Automation Journey
In the end, automation is an obvious contributor to cost savings because it reduces setup costs, machine downtime, and labor costs. It also reduces production run times by combining operations into a single setup or leveraging gang slides and turrets to run several limited production parts consecutively. At Absolute Machine Tools, our A+ Automation Team works with North American manufacturers to find the best solution possible for their needs. Contact us today at info@absolutemachine.com.